Can laser welding equipment really replace traditional welding in modern manufacturing workflows?
In today’s highly competitive manufacturing landscape, the question of whether laser welding equipment can truly replace traditional welding methods is no longer just theoretical—it’s central to operational strategy. With industries demanding higher precision, faster output, and minimal downtime, welding processes are evolving. Yet, transitioning to laser-based systems is more than just swapping one machine for another. It’s a fundamental shift in how metal fabrication and component joining are approached.
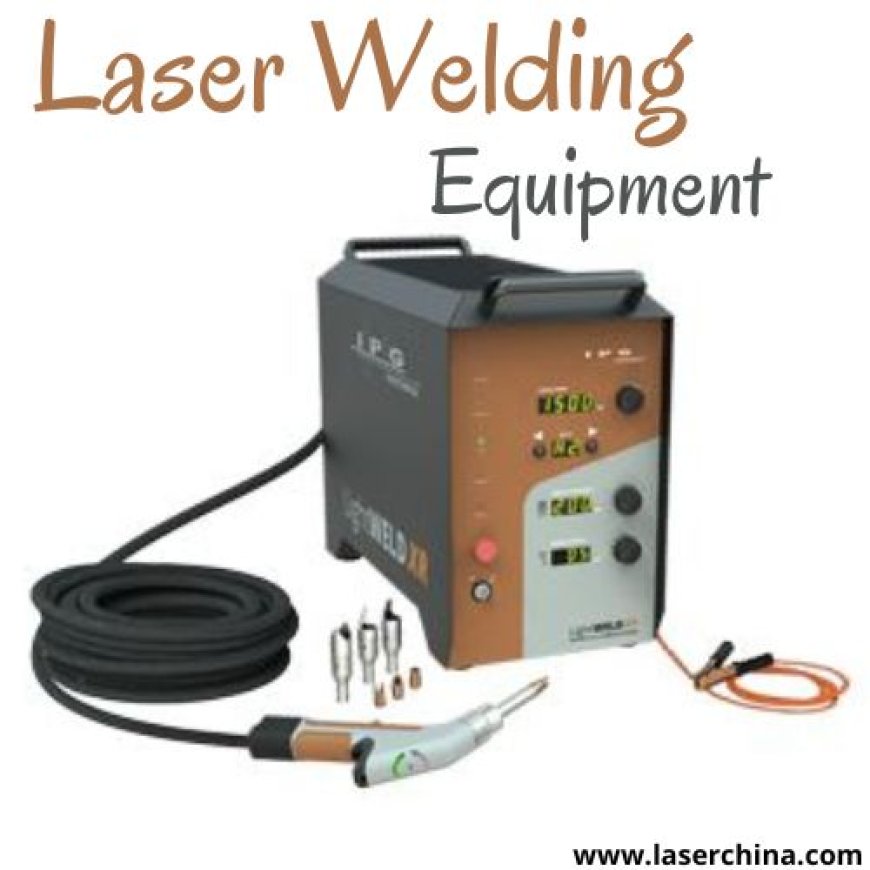
Let’s explore this transformation in depth and understand how laser welding equipment fits into the real-world industrial puzzle.
The Industrial Shift Toward Precision
Industries like automotive, aerospace, electronics, and medical devices now require joining techniques that ensure minimal thermal distortion, deep penetration, and high repeatability. These sectors have low tolerance for errors and demand cleaner joints with stronger metallurgy. This is where laser welding equipment begins to change the conversation.
Unlike traditional arc or TIG welding, laser welding uses a highly concentrated beam of light to fuse materials. The energy density is immense, allowing for narrow welds with excellent depth-to-width ratios. But what makes this shift more than just a technical upgrade is the way it reshapes entire production processes.
Manufacturing Efficiency Redefined
Modern production lines are often automated, monitored, and optimized for precision. In such environments, equipment that requires constant manual intervention or that produces variable results becomes a bottleneck. Laser welding equipment is designed for integration into automated cells, robotic arms, and smart factory ecosystems.
For example, a robotic welding cell fitted with laser systems can join multiple parts in a single pass, often without the need for post-processing like grinding or cleaning. This doesn’t just save time—it changes the timeline of production entirely.
In traditional welding, distortion from heat input often requires extra fixturing or secondary processing. With laser systems, the heat-affected zone is significantly smaller, which reduces deformation. This allows for leaner fixtures and better dimensional control—elements that matter deeply in industries that operate at scale.
Real-World Application: Automotive Industry
To illustrate, let’s consider how automotive manufacturers are adopting laser welding equipment in key structural areas of vehicles. One critical zone is the body-in-white (BIW) structure—the skeletal frame of a car. Here, laser welding is used for:
-
Roof-to-side panel joins
-
Tailor-welded blanks
-
Battery enclosures in electric vehicles
These applications require both aesthetic finish and structural integrity. Conventional spot welding creates multiple heat points and visible marks. In contrast, laser seam welding delivers a clean, almost invisible line with uniform penetration and superior strength.
The adoption of laser welding equipment in this space is not merely optional anymore—it’s becoming a competitive requirement. Car brands are now marketing the tight tolerances and clean joints enabled by lasers as part of their premium build quality.
Aerospace and the Demands of Material Science
In aerospace, every gram of weight and millimeter of structural integrity counts. Whether it’s titanium, Inconel, or advanced aluminum alloys, the ability to join dissimilar or heat-sensitive metals without contamination or warping is critical.
Laser welding equipment supports these needs with pinpoint accuracy. It allows engineers to experiment with thin-walled structures, honeycomb panels, and non-ferrous metals—all of which are standard in aircraft design.
Also, the aerospace industry often deals with low-volume, high-complexity parts. Manual welding would require a skilled workforce and may introduce variability. Laser welding, integrated with CAD and simulation software, creates repeatable, certified-quality welds. It aligns perfectly with the regulatory and safety demands of this high-risk industry.
Compact Powerhouses: Electronics and Medical Devices
While heavy industries benefit from high-output laser systems, precision industries use smaller-scale laser welding equipment for micro-welding applications. Take electronics, for example. From lithium battery cells to connectors, sensors, and microcircuits, components are shrinking—but performance expectations are growing.
Traditional methods either can’t reach these tiny joints or produce too much heat, risking damage. Laser systems equipped with beam steering and high-resolution focus control can weld wires as thin as a human hair or enclosures smaller than a coin, all with surgical precision.
Similarly, in the medical device sector, components like catheters, stents, and surgical instruments require sterile, smooth welds without oxidation or porosity. Laser welding creates hermetic seals and bio-compatible joints that pass rigorous FDA and ISO standards.
From Manual Labor to Intelligent Control
Welding has traditionally been considered a skilled trade. But as manufacturing shifts towards digital control and data-driven quality assurance, the role of the welder is also evolving.
Laser welding equipment is not just a machine—it’s part of a control loop. Parameters such as beam intensity, pulse frequency, weld speed, and focal distance are monitored and adjusted in real-time. This feedback control enables zero-defect production, traceability, and predictive maintenance—none of which are possible with manual arc welding.
Even more, many laser systems come with vision systems and sensors. These allow for real-time tracking of joint location and compensation for part misalignment. This minimizes human error, especially in large-volume applications.
Sustainability and Material Savings
Environmental responsibility is no longer just a branding concern—it’s part of corporate compliance and strategy. Laser welding equipment supports greener operations in several ways:
-
Material efficiency: Less filler material is needed. In many cases, none.
-
Lower energy consumption: Compared to resistance or arc welding, lasers use energy more efficiently.
-
Minimal rework: Higher first-pass yield means less scrap and less reprocessing.
This efficiency translates into lower operational costs, better resource management, and alignment with global sustainability goals—especially for export-oriented manufacturers.
Adaptation, Not Replacement
Does all this mean traditional welding is obsolete? Not exactly. In heavy construction, pipeline welding, and shipbuilding, where environmental conditions are harsh and portability is key, arc and MIG welding still dominate.
However, what’s becoming clear is that laser welding equipment doesn’t just replace traditional methods—it fills a void those methods were never designed to serve. It expands the envelope of what’s possible in design, speed, accuracy, and scale.
For manufacturers that want to stay ahead, adding laser technology isn’t about abandoning the past. It’s about integrating precision into the future.
Final Thoughts
Laser welding equipment has evolved from a niche innovation into a cornerstone of smart manufacturing. From boosting efficiency and repeatability to enabling micro-scale welding and complex material joining, it delivers performance traditional welding can’t match. Its role is no longer experimental—it’s essential.
In industries where quality, precision, and speed are non-negotiable, relying solely on traditional welding can limit innovation and productivity. Embracing laser welding equipment is not just a technical upgrade; it’s a strategic move that aligns with the demands of modern engineering and global competitiveness.
Whether you’re a production engineer looking for tighter tolerances, a procurement officer considering ROI, or a decision-maker exploring smart manufacturing tools—laser welding equipment is a technology you can no longer afford to overlook.